工場におけるIoTの導入とその価値
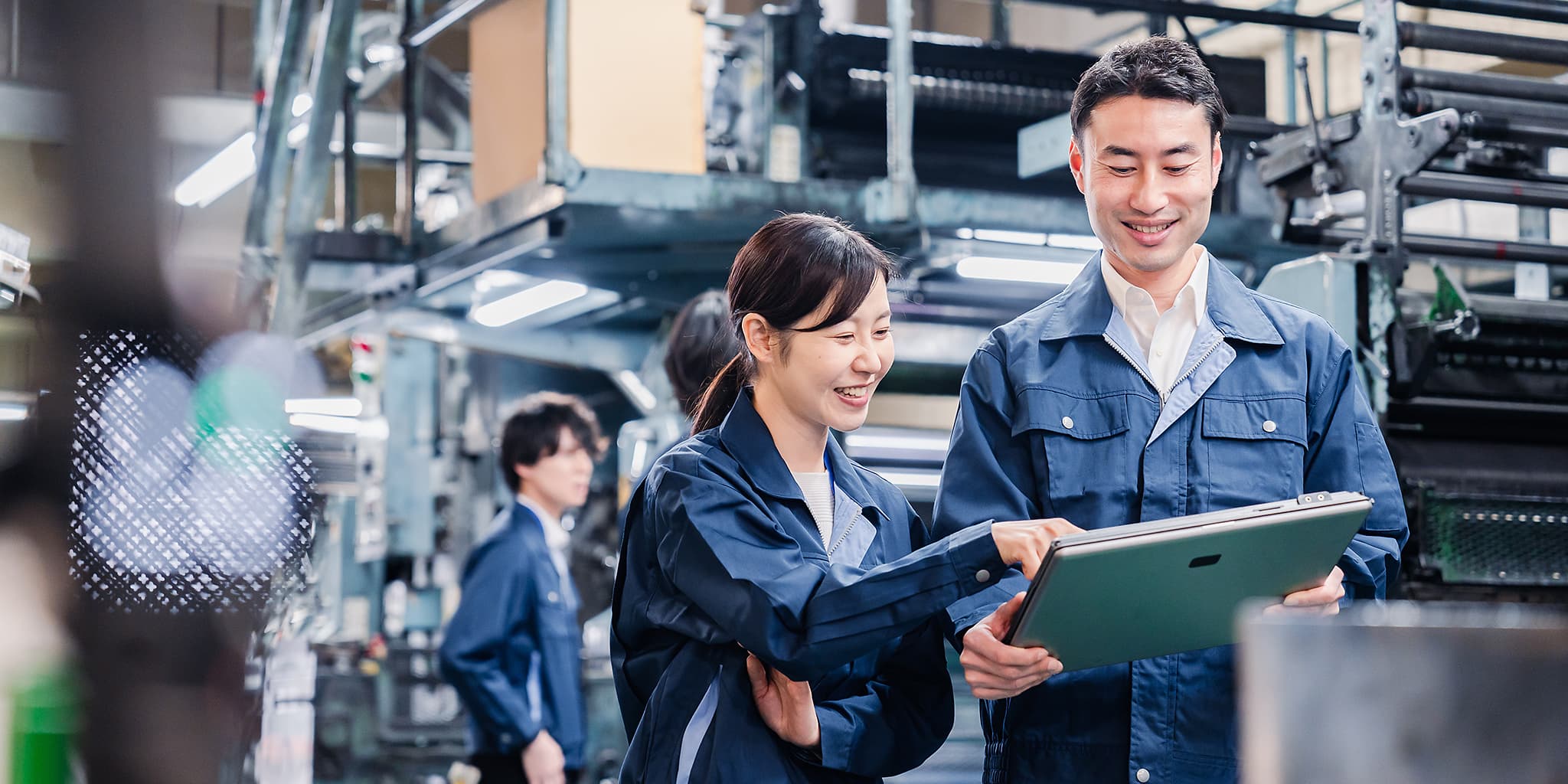
製造業における重要な3つの要素は、「QCD管理」「自社製品・サービスの付加価値向上」「新たなビジネス創出」です。工場の生産管理のQCD管理は、「所定の品質・仕様」(Quality)の製品を「所定のコスト」(Cost)で、「所定の数量・納期」(Delivery)どおりに生産できるよう生産活動を管理するという3つの要素が存在します。この一連の流れをQCD管理と言い、効率的に行うことが生産管理の目的で、3つの要素をバランスよく達成することが重要です。
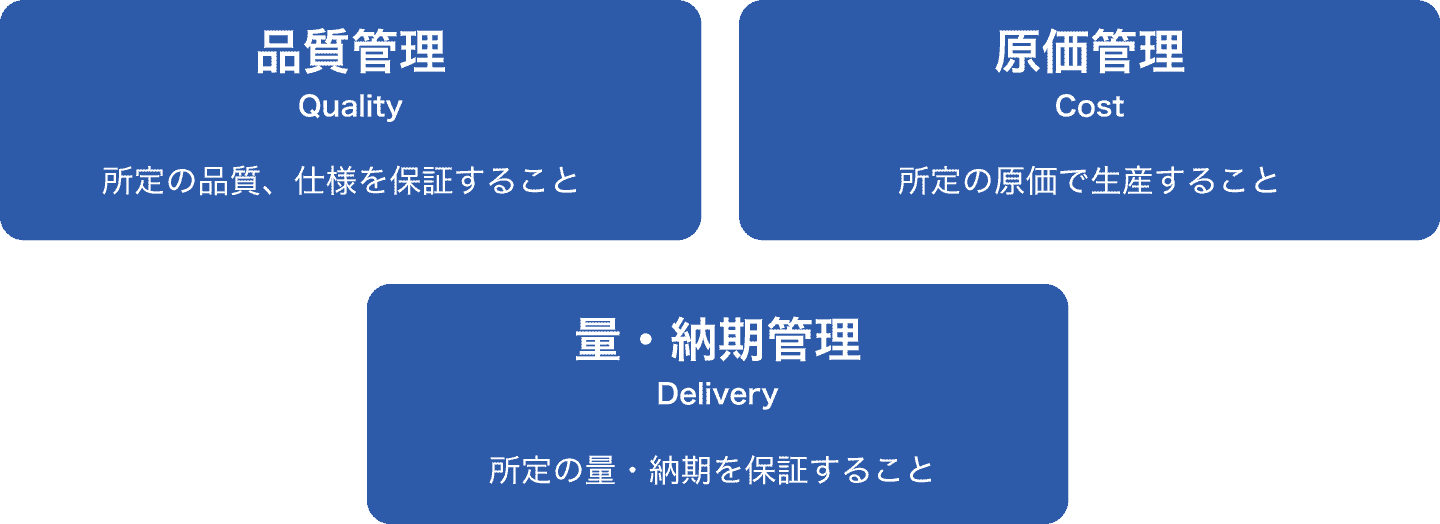
自社製品・サービスの付加価値向上では、機能の向上やユーザーにとっての利便性向上を目指します。新たなビジネス創出では、自社で開発し、活用しているスマート工場の仕組み(システム)を外板するなどが可能性として存在します。この記事では上記の3つの要点につながるように、工場の生産性向上におけるIoT活用について解説します。
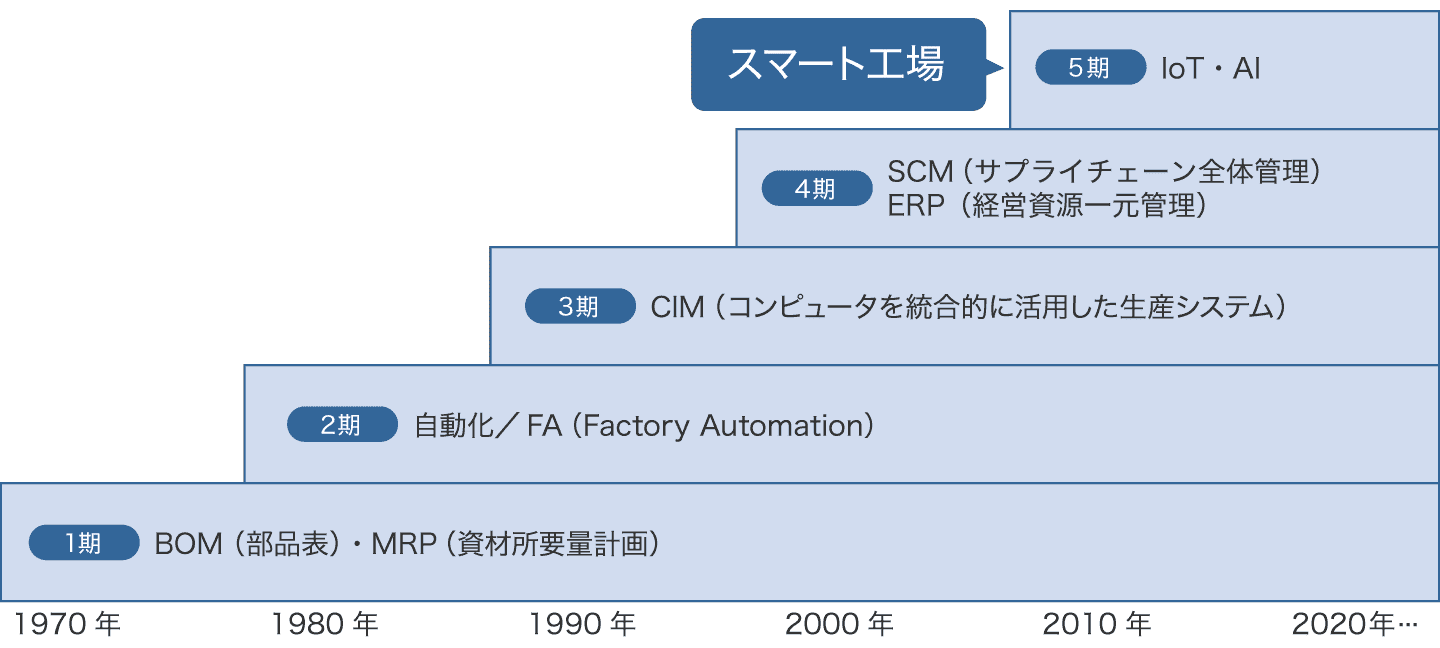
工場とIoTの現状と導入背景
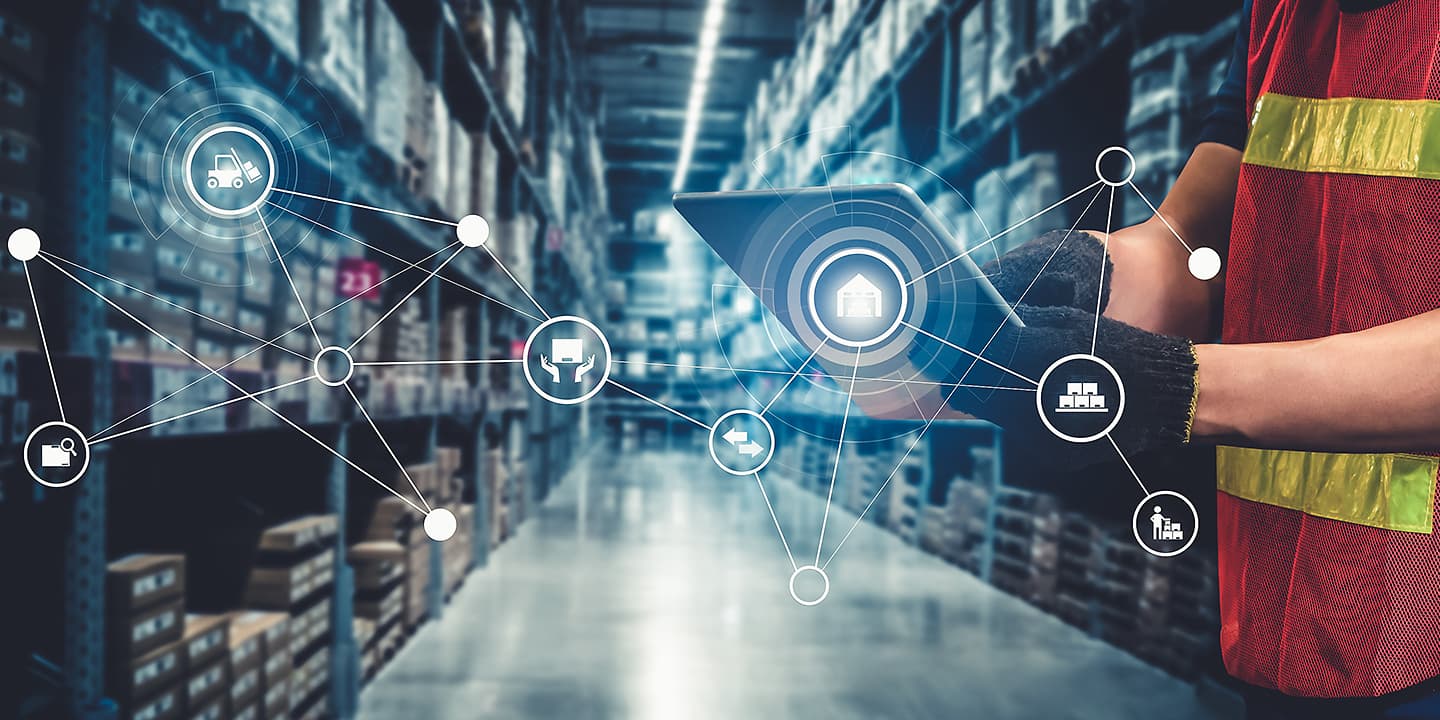
工場には「エンジニアリングチェーン」と「サプライチェーン」の2つの業務チェーンがあります。エンジニアリングチェーンを支える情報システムは図のようにPDM、CAE、CAD・CAMのデータに集約されます。サプライチェーンは、需要予測システム、ERP、APS・スケジューラ、TMS、MES、WMSなどが存在します。中間に存在するマスターとデータベースでは、品目マスター、E-BOM、M-BOM、取引マスター、在庫マスターが中継役として存在します。
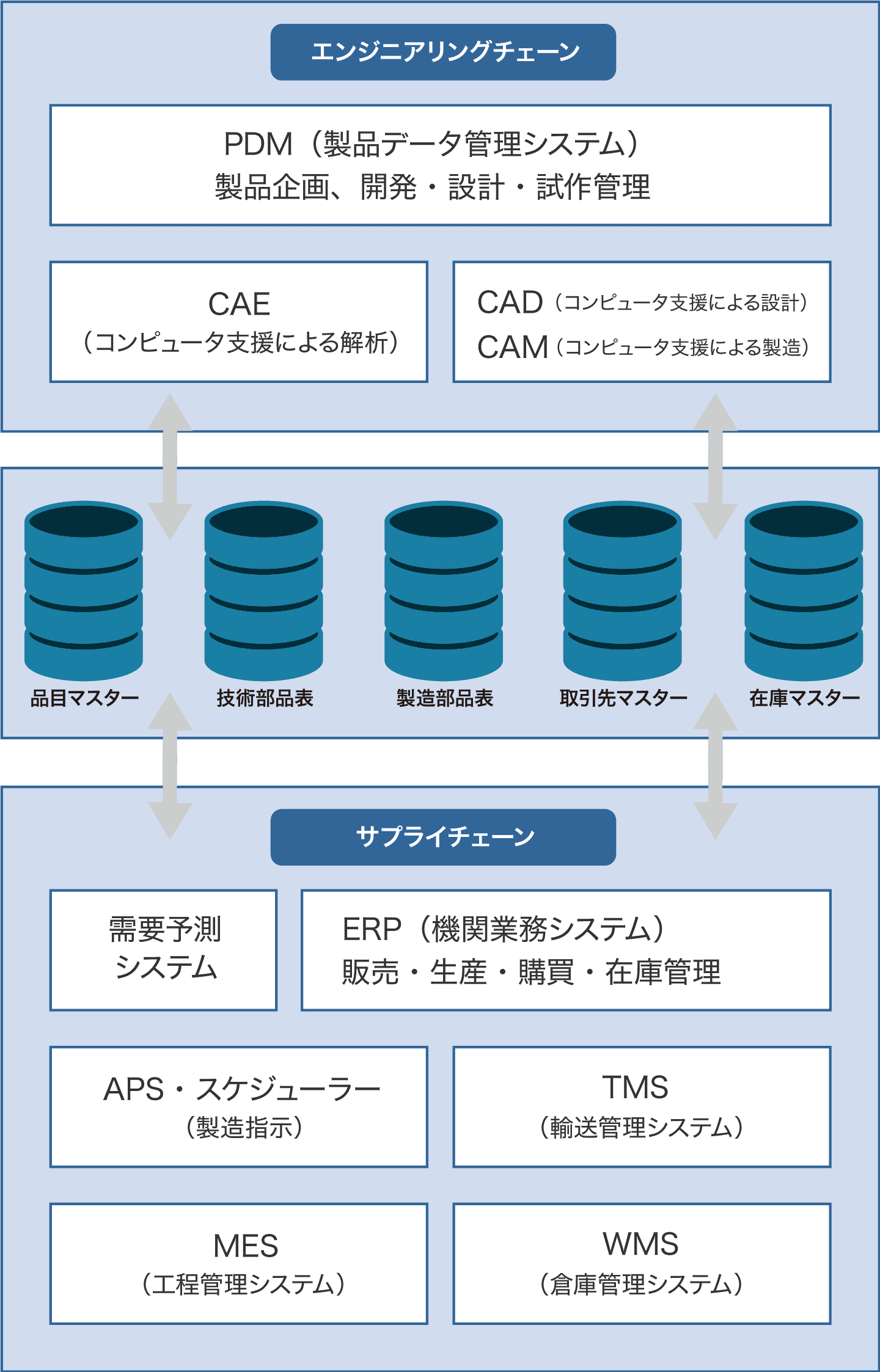
工場におけるIoTの導入背景
エンジニアリングチェーンは、「製品企画 → 開発 → 設計 → 試作 → 量産立ち上げ」の順番で進められますが、コンピュータが高度化するに連れ、業務内容は大きく変わってきました。三次元の設計図を描き、デジタルモックアップ(仮想試作)が行われ、製品のデザインや機能性、組立の効率性などを評価しています。サプライチェーンは、「需要予測に基づいて生産計画を立て、生産計画に基づいて生産し、受注に基づいて製品を納品する」流れでは昔も現代も変わりませんが、顧客ニーズは大きく変化しています。現在では顧客や市場の要求が多様化し、さらに短納期での納品が求められるようになりました。多品種少量生産の時代を迎えた今、市場ニーズを俊敏に捉え、顧客の希望する納期で納品しなければ購入をしてもらえない厳しい時代です。両者の連携を高度化するためには情報システムの活用は不可欠です。
IoTと製造業の相互作用
IoTは製造に位置するエンジニアリングチェーンと顧客ニーズに応えるサプライチェーンの高度な連携で活用できる技術です。PLM(Product Lifecycle Management:製品ライフサイクル管理)は、製品に関するすべての情報(製品構成、技術情報、プロダクト管理、在庫、売上など)を共有化し、全業務のプロセスにわたって製品の収益管理を行います。関連するサブシステムには以下のようなものがあります。
略称 | 英語表記 | 説明 |
---|---|---|
CRM | Customer Relationship Management | 顧客から直接的な機能要求や品質情報を入手するシステムで、製品の品質向上や次期製品のための有益な情報を研究開発や製品企画に提供できます。 |
SRM | Supplier Relationship Management | 市場動向に併せた柔軟な供給体制のための機能で重要取引先との協業には必須です。 |
SCM | Supply Chain Management | 資材の供給連鎖管理のことで、優秀なサプライヤーの確保、購入単価の低減、購買業務効率の改善などを目的としています。 |
ERP | Enterprise Resource Planning | 製品の主要な原価要素が管理されており、PLMの中の大部分の収益を管理する重要なシステムです。 |
MES | Manufacturing Execution System | 製品コストの3要素である材料費、労務費、経費の実績を収集する原価計算の根幹となるシステムです。 |
PDM | Product Data Management | PLMプロセスの核となるシステムであり設計・開発業務全般の管理と製品に関する技術情報を一元的に管理しており、製品の収益性向上に重要な役割を担っています。 |
新製品が発表するまでには、開発費用や試作品の生産など、多額の先行投資が必要で、これを回収した後にやっと利益が生まれます。先行投資を回収するまでの期間(リードタイム)が短ければ、利益が生まれやすくなります。PLMにはTTP(Time To Profit)開発着手から開発費回収までの期間、TTV(Time To Volume)量産立ち上げまでの期間、TTM(Time To Market)新製品を市場に出すまでの期間の3つの要素が存在します。
略称 | 英語表記 | 説明 |
---|---|---|
TTP | Time To Point | 開発着手から開発費回収までの期間のことです。期間を短縮することで、収益期間を伸ばします。 |
TTV | Time To Volume | 量産立ち上げまでの期間です。儲かる時に売り切ってしまうなどムダのないビジネス展開が可能になり、収益増加に繋がります。 |
TTM | Time To Market | 新製品を市場に出すまでの期間です。市場ニーズを捉えてタイムリーに新製品を世に送り出すことが重要です。 |
IoTが解決する課題とは?
工場における課題は、俯瞰的に考えるとエンジニアリングチェーンとサプライチェーンのデータ活用と連携です。データ活用によりIoTで解決する内容も数多く存在します。
エンジニアリングチェーンプロセスでは、以下の手順で会社として持っている技術力、知識、経験、ノウハウを体系的に共有化し評価をします。
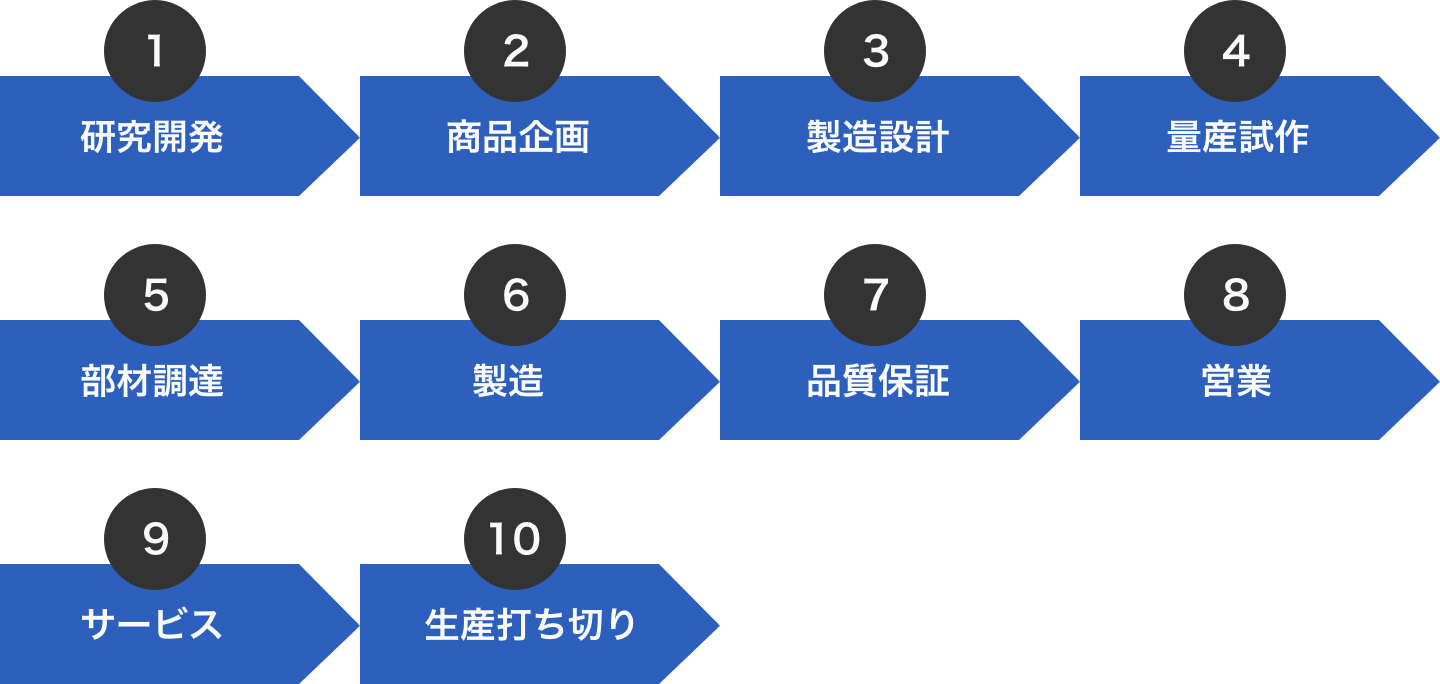
サプライチェーンプロセスでは、市場、顧客、需要情報の順で考える「ERP」の計画システムと、生産、在庫、供給情報で考える実行システムが存在します。
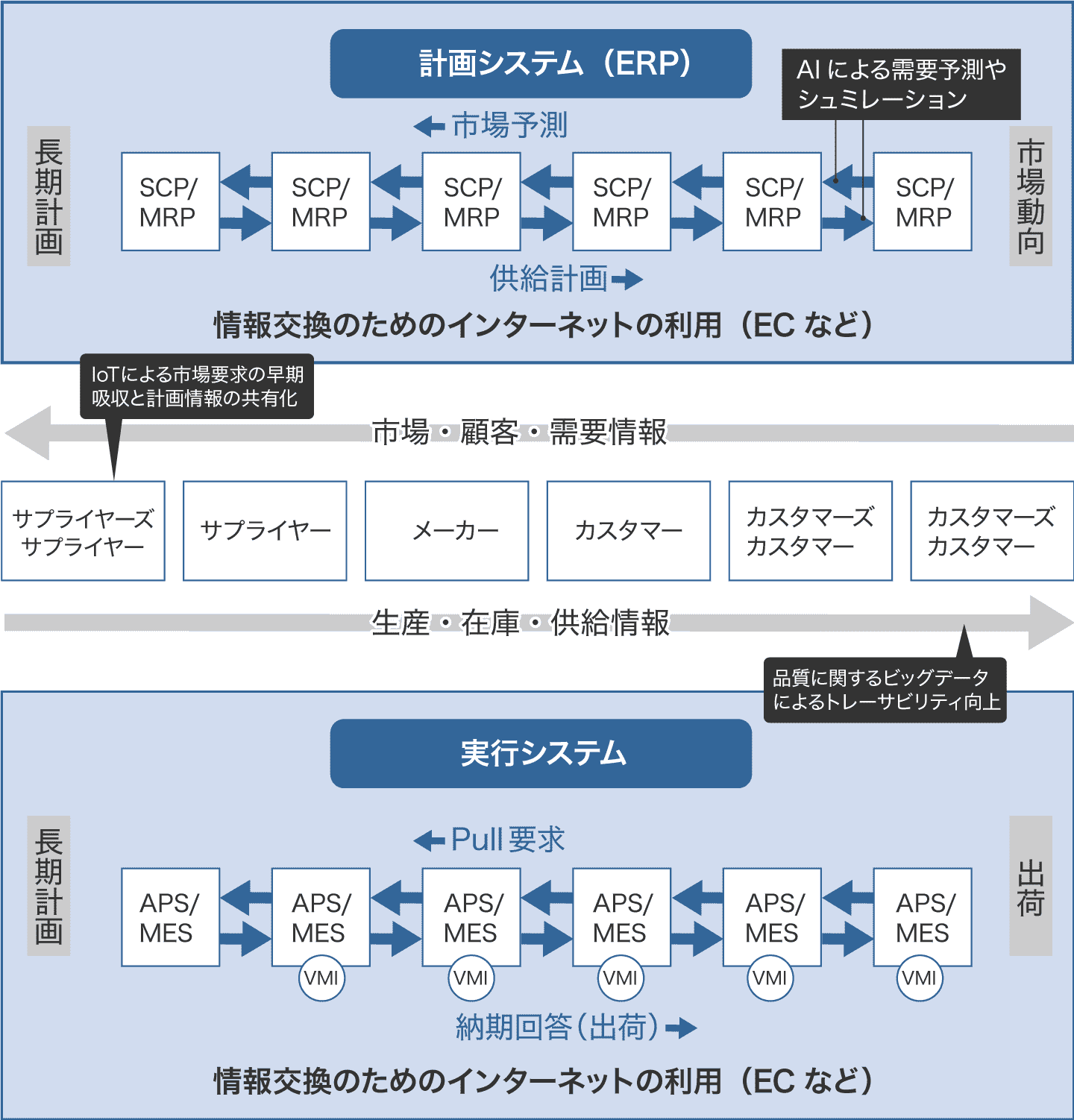
略称 | 英語表記 | 説明 |
---|---|---|
SCP | Supply Chain Planning | サプライチェーン・マネジメント計画 |
MRP | Material Requirement Planning | 資材所要量計画 |
APS | Advanced Planning and Scheduling | 先進的生産計画&製造スケジューリング |
MES | Manufacturing Exection System | 製造実行システム |
工場のIoT化とその意義
エンジニアリングチェーンを縦軸とサプライチェーン横軸のビジネスプロセスを図解して考えます。縦軸のエンジニアリングチェーンでは各工程でのデータを集約します。横軸のサプライチェーンでは経営や管理と工場の現場と仕入先から顧客ニーズの流れで集約しています。双方を連携して見える化することで、改善する課題が発見できます。
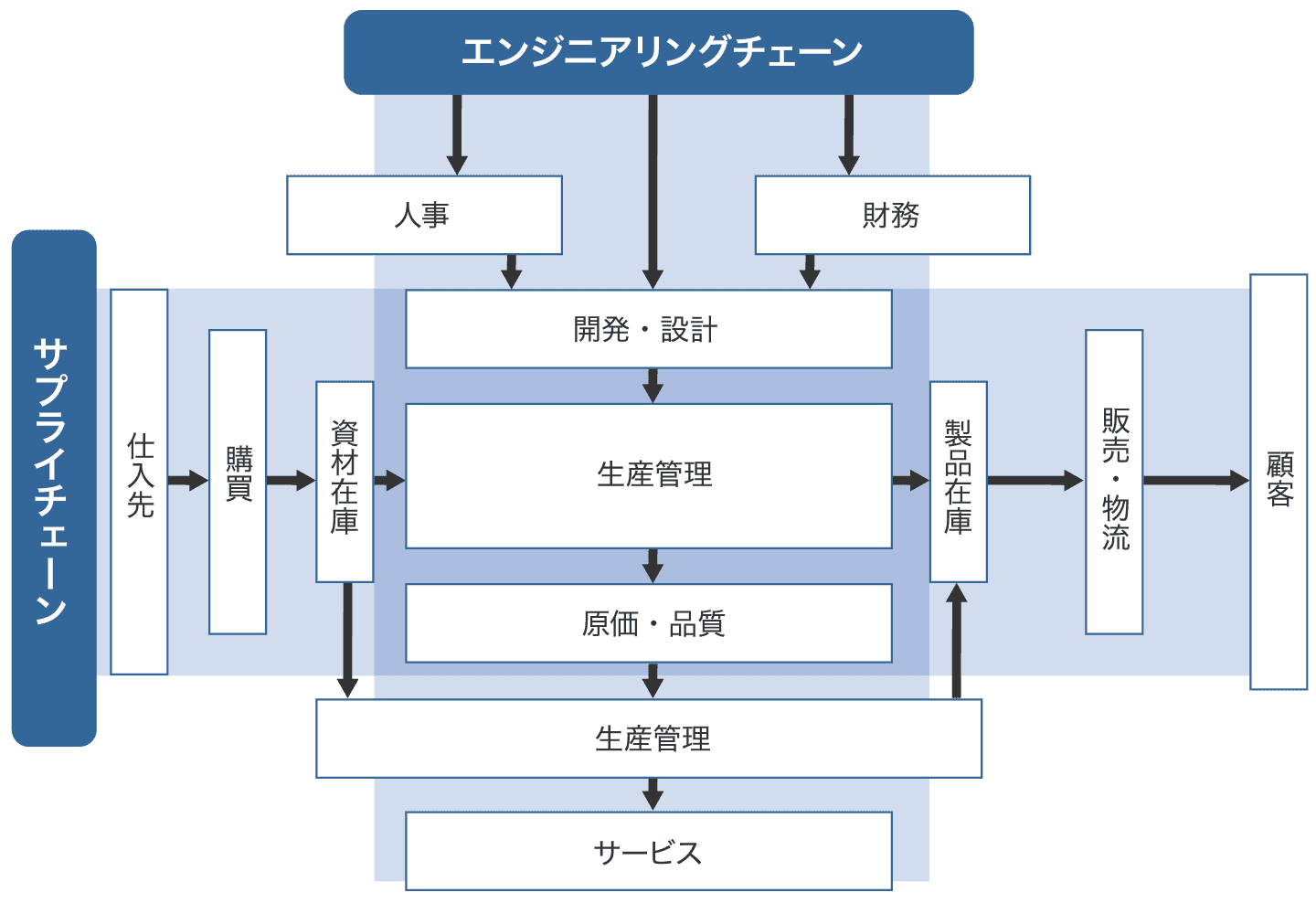
IoTを通じた工場変革とスマートファクトリーの実現

ドイツが産んだ「インダストリー4.0」は2011年から始まった製造業の革新です。日本でも取り組まれており、IoTによるビッグデータの収集と、それを学習したAIによる分析と制御を通じて、自ら考えるスマートファクトリーの実現が第4次産業革命と呼ばれているものです。
IoTを導入したスマートファクトリーは、新しいシステムを導入した工場というわけではありません。製造業の業務そのものに変化があるわけではなく、それを支えるハードウェアやソフトウェアが高性能になり、ICT(情報通信技術)の活用が盛んになると考えたほうが良いでしょう。クラウドコンピューティングで機能をスムーズに活用するには、インターネット上のデータの取扱いに関する規約(XMLやXHTMLなど)、そして生産設備からの情報収集に関する通信プロトコルや内容に関する標準化等の整備を進める必要があります。IoTを導入したスマートファクトリーシステムでは、主に図のようなイメージで一元管理ができます。
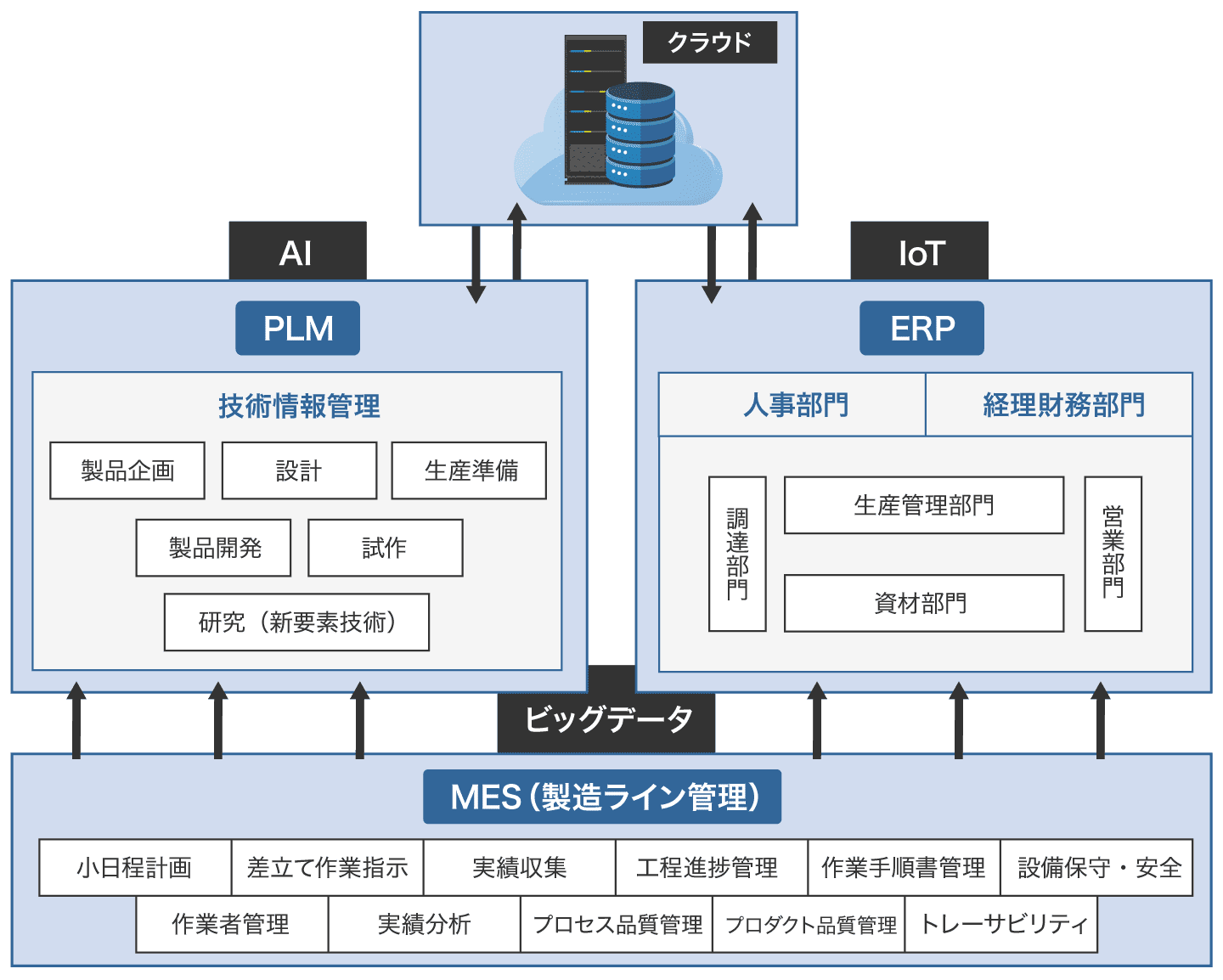
生産設備の変革、IoTの影響
IT関連技術の進歩において、製造業では規模、業種を問わず「見える化」が広がってきました。工場の見える化とは、目で見ることができない工場の生産活動情報を、IT技術やセンシング技術を活用して適切に表すことをいいます。
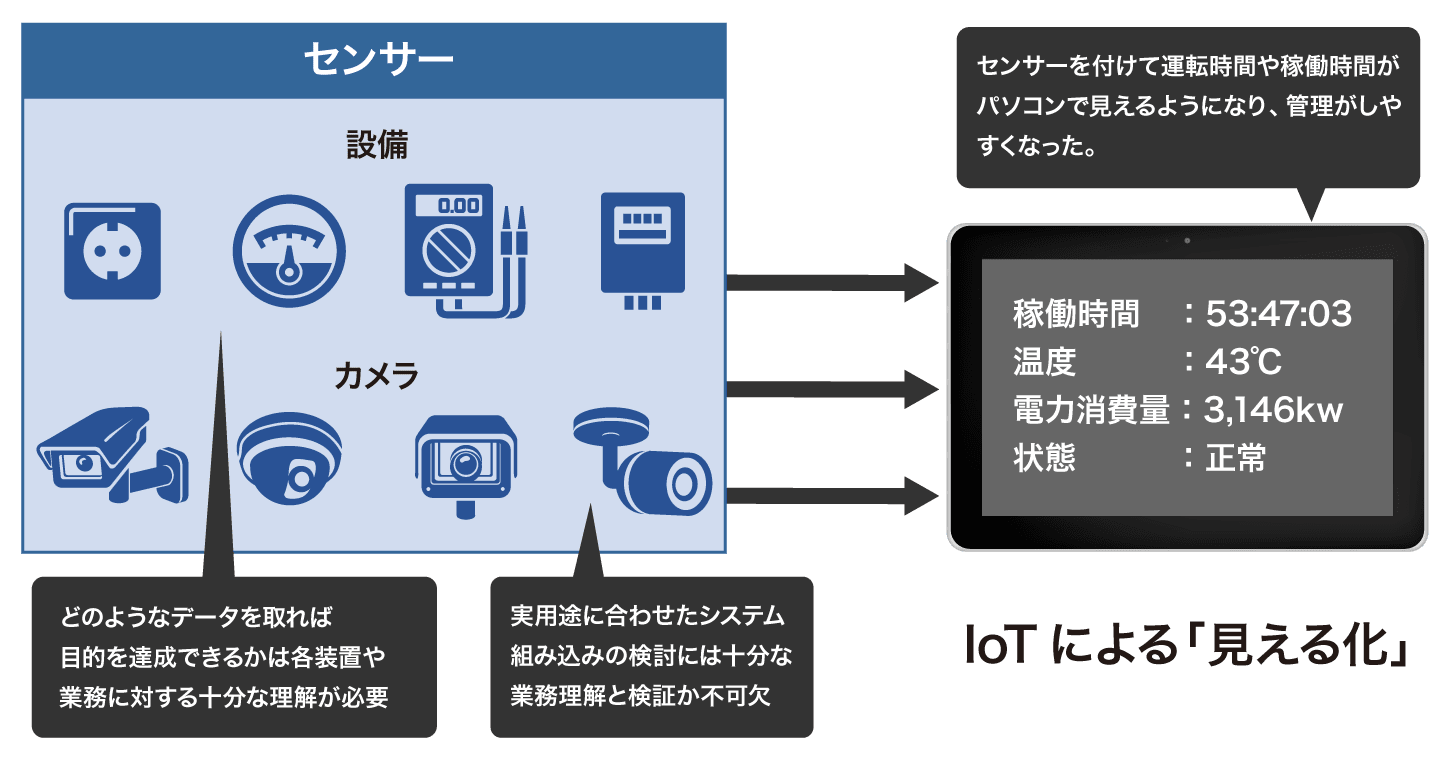
見える化情報を活用した現場へのフィードバック
様々な生産活動を見える化しデータ化を行ったら、製造現場へ情報を提供する必要があります。
- 製造現場で異常が起こった際に速やかに対応するため、担当者のスマートフォンへ設備の警告情報をリアルタイムに届けるシステム
- 作業者の配置を最適化するために、計画と実績を比較できるよう情報をひと目でわかるように表示するシステム
- 装置の状態情報をリアルタイムで収集することによって、人が判断していた製品の良否を自動的に検出するシステム
現場で収集したデータを見える化してフィードバックをすることで、生産活動を最適にコントロールする業務運用が期待できます。より大きな効果を得るためには、製造、設計間で製造上の課題を共有し、調達部品の要求期限を最適化するなど、設計部門や調達部門もフィードバックの範囲を拡大することが大切です。
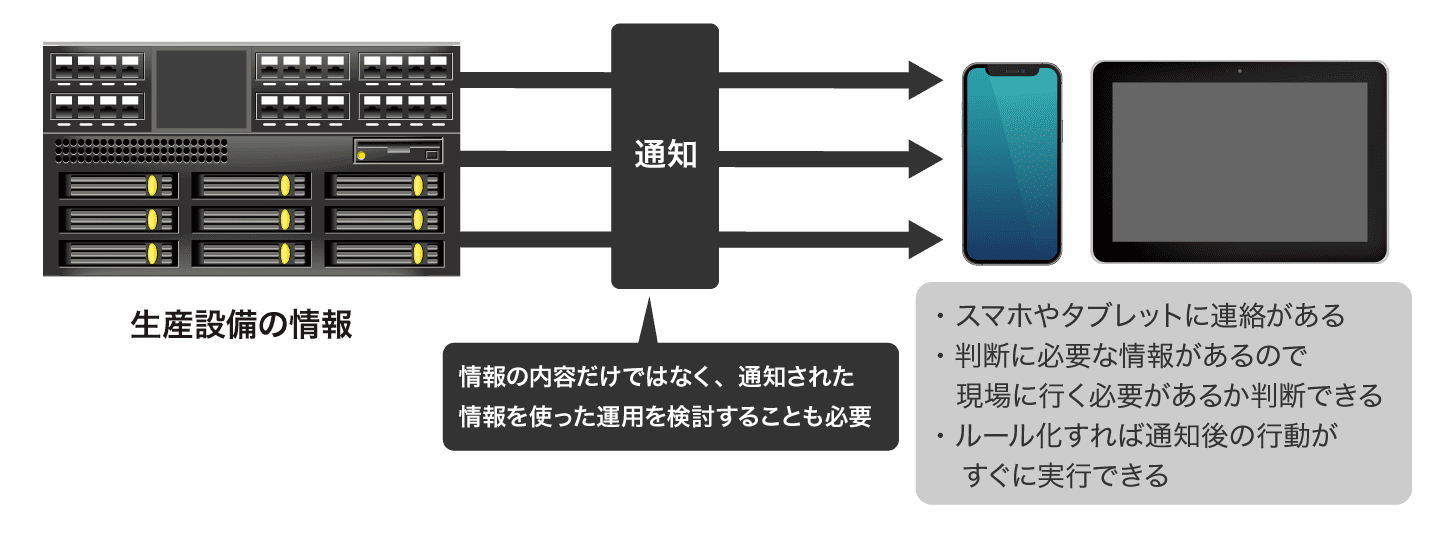
データ収集と分析の進化(AIの活用)
データ収集で分析をするにはAIの活用が有効です。AIを利用することで、現在明確になっていない課題の抽出や、将来の予測精度の向上にも活用することができます。IT関連技術の進歩で、従来では収集することが困難だった様々な装置の情報を、製品や人、装置や材料に結びつけて収集することが容易になりました。AIの技術発展によって、従来ルール化や解析が困難なために人が担ってきた判断業務の自動化ができるようになってきました。
- サンプル工程情報を大量に学習させて、サンプル工程を設定した工程設定者と同じような工程を自動的に設定する。
- 不良率や稼働率といった改善目標にたいし、関連が明確ではない大量データを収集し、どのデータをコントロールすれば目的を達成できるのか分析する。
このような取り組みによって、従来ベテランの従業員が実施してきた判断業務を自動化し、人間が気づけていなかった新たなルールを発見できるようになってきました。また、将来を推定するためにシュミレーターで予測情報を得ることもできます。データを収集することが容易になってきたので、最新データを首位レータの前提条件にフィードバックすることで、予測を実態に合わせて精度向上させることも可能になってきています。万能なAIやシュミレーターは存在しませんが、一定の条件下で適用できるAI技術などを活用した事例も徐々に増えつつあります。
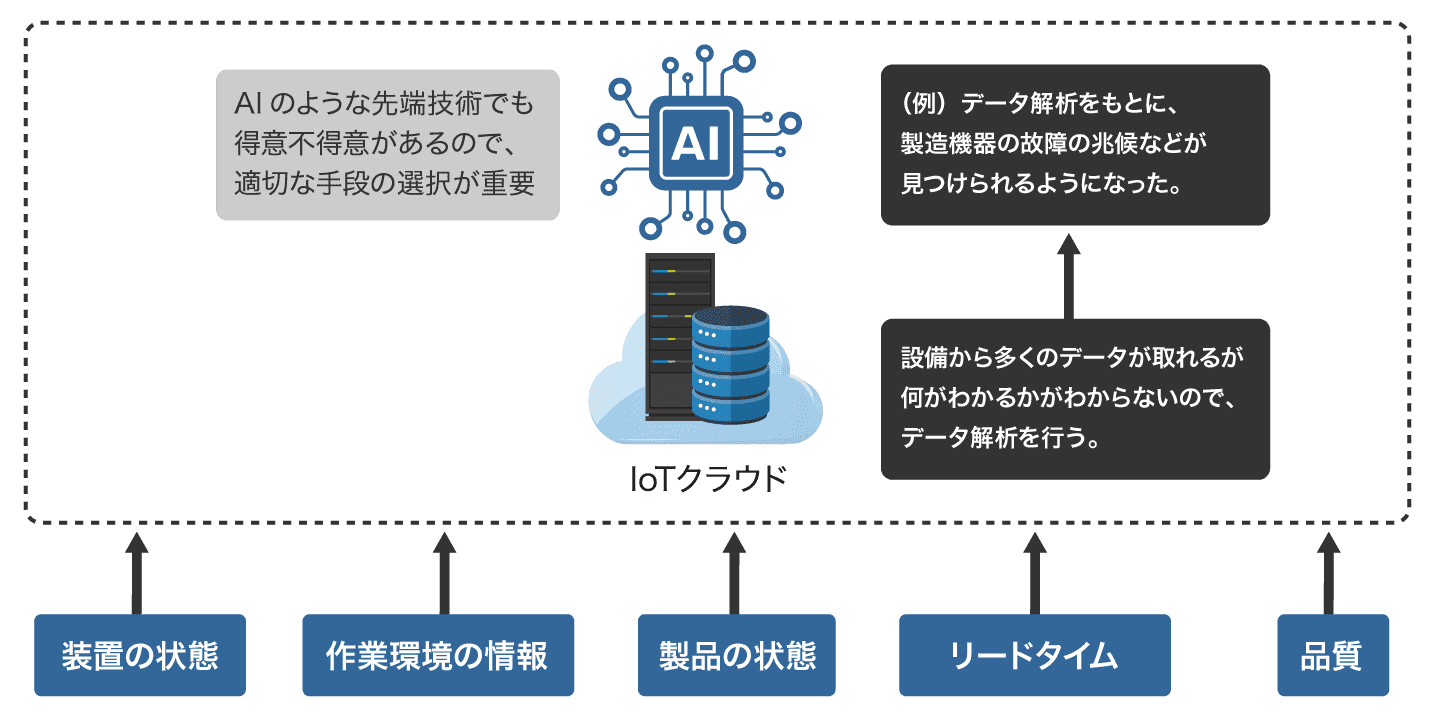
工場内の自動化と効率化
例えば工場内の自動化や効率化の目的は、工程調整や生産計画の自動化でリードタイムを軽減することも必要とされます。RFID(Radio Frequency IDentifer)タグを用いた見える化システムで、全体工程の日程調整時の各工程の負荷調整、現場課題抽出と対策、日々の負荷調整といった現場管理監督者の意思決定に依存するプロセスに対して、判断のノウハウを定型化し、システムに折り込むことで、誰でも均一に判断できるようになります。
また、生産自動化について、産業用ロボットを活用した例も存在します。産業用ロボットを多用して無人化することで、人間による作業ミスの軽減、作業効率や人間の安全性向上を目的としています。デジタル上に製品や生産ラインを再現し、それを自動生産に繋げる技術の実用化は、製造業界でも始まっています。
スマート工場の実現とその価値
主に、生産性向上、品質向上、コスト削減、柔軟性向上、安全性向上の価値が得られます。スマート工場の実現には、IoTやAIなどの最先端技術の導入に加え、現場の業務プロセスや組織体制の改革なども必要となります。これらの課題を克服することで、工場の競争力を高め、新たな価値を生み出すことができます。今後はスマート工場の実現により、製造業の競争力を高めるための重要な要素になると期待されています。
工場IoT導入の課題とその解決策
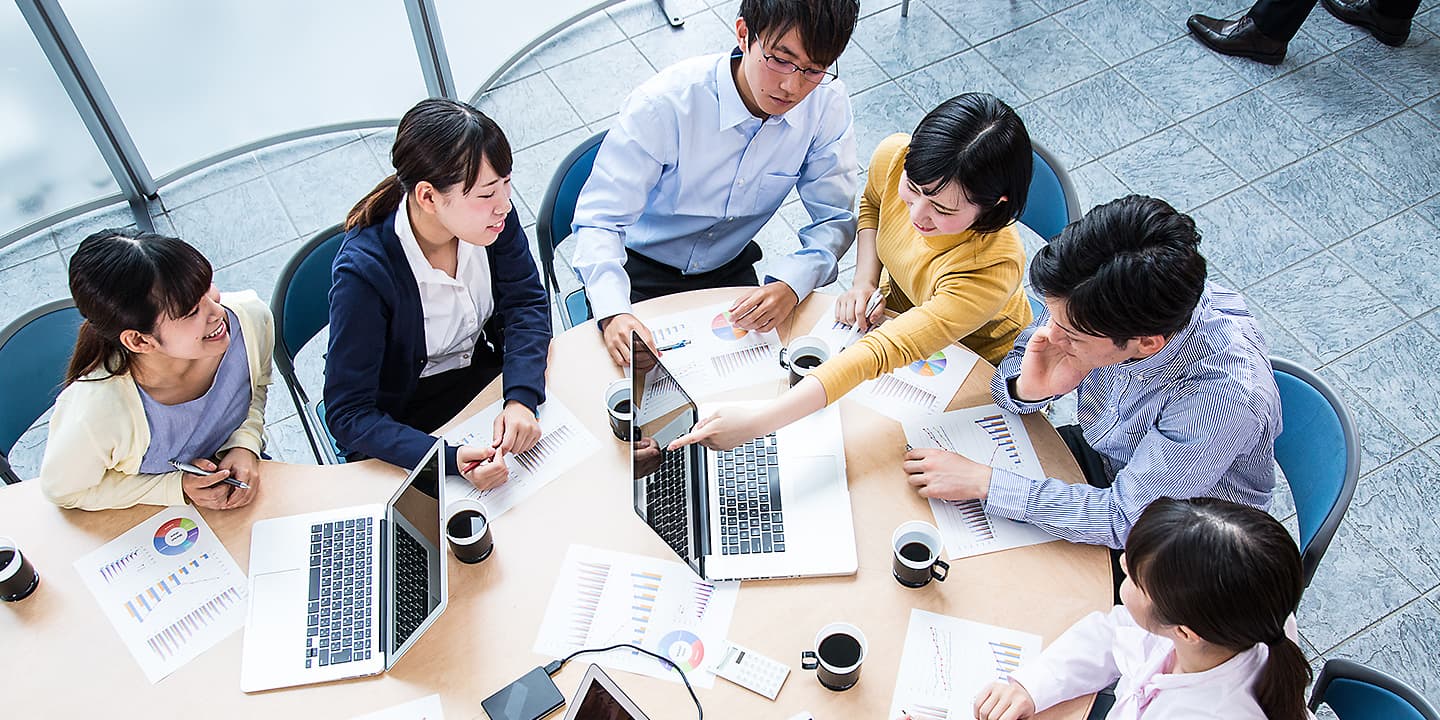
工場IoT導入の課題は大きく分けて、導入コスト、人材不足、セキュリティリスクの3つが挙げられます。特に人材不足では、製造業における先端技術を活用する専門知識や技術を持った人材が不足していることが深刻な問題となっています。IT人材不足を解消するために、社内でのIT人材育成や、外部人材の活用を検討することが必要とされます。また、IoTやAIを活用した業務プロセスの自動化や省人化を進めることで、人手不足の負担を軽減することも可能です。導入コストやセキュリティの課題は、次の小項目で説明します。
初期コストの問題と打破
初期投資はセンサーやカメラなどのIoTデバイス導入、データ収集・分析のためのシステム構築、データ活用のためのアプリケーション開発が当てはまります。維持管理コストは、導入したIoTデバイスの運用・保守による定期的なメンテナンス・点検、システムの運用・保守にかかるコストが中心です。初期投資だけでも製造業では一般的に数百万円から数千万円の多額の予算が必要とされるため、維持管理費を含めて導入後の効果測定は、導入コストと導入によって得られる効果(ROI)をもとに計算をして評価をすると良いでしょう。

IoTメンテナンスの重要性
主に、予兆検知による故障防止、メンテンナンスの最適化、メンテナンスの効率化が重要です。設備の稼働率や品質の向上、メンテナンスコストの削減など様々なメリットをもたらすことができます。具体的には、設備の稼働状況をリアルタイムで把握することができるため、予兆検知による事故防止に繋がります。また、IoTデータを活用することで、設備の劣化状況を把握し、適切なメンテナンスのタイミングを判断することができます。メンテナンス頻度や内容を最適化し、コストや人的負担を軽減できます。さらには、メンテナンス作業を自動化したり、遠隔で実施することで、効率化を図り、作業員の負担軽減につながることも期待できます。
古い生産設備へIoTの適用
IoT適用する際には、設備の状態、セキュリティ対策、運用体制に注意することが必要です。古い設備は故障や劣化が進んでいる可能性がありますので、設備の状態を十分に確認し、IoT適用可能であるか検討する必要があります。古い設備を継続して利用する具体的な方法は、レトロフィットIoTと呼ばれるセンサーやカメラなどのデバイスを後付してIoT化を実現する方法です。既存の設備をそのまま使用できるため、設備の更新に伴う大きなコストや工期を抑えることができます。
IoTと工場環境のセキュリティ問題・対策
工場内の設備やシステムがインターネットに接続されることで、サイバー攻撃のリスクが高まります。サイバー攻撃から守るために、セキュリティ対策を徹底します。システムのサイバーセキュリティは、ファイヤーウォールやIPSなどのセキュリティ機器の導入、データの暗号化、アクセス権限の制限などで対策を講じます。工場IoTのセキュリティポリシーの策定、対策の実施、運用の手順で進め、定期的に点検・改善を実施することで効果を維持することができます。
工場のIoT化導入ステップ
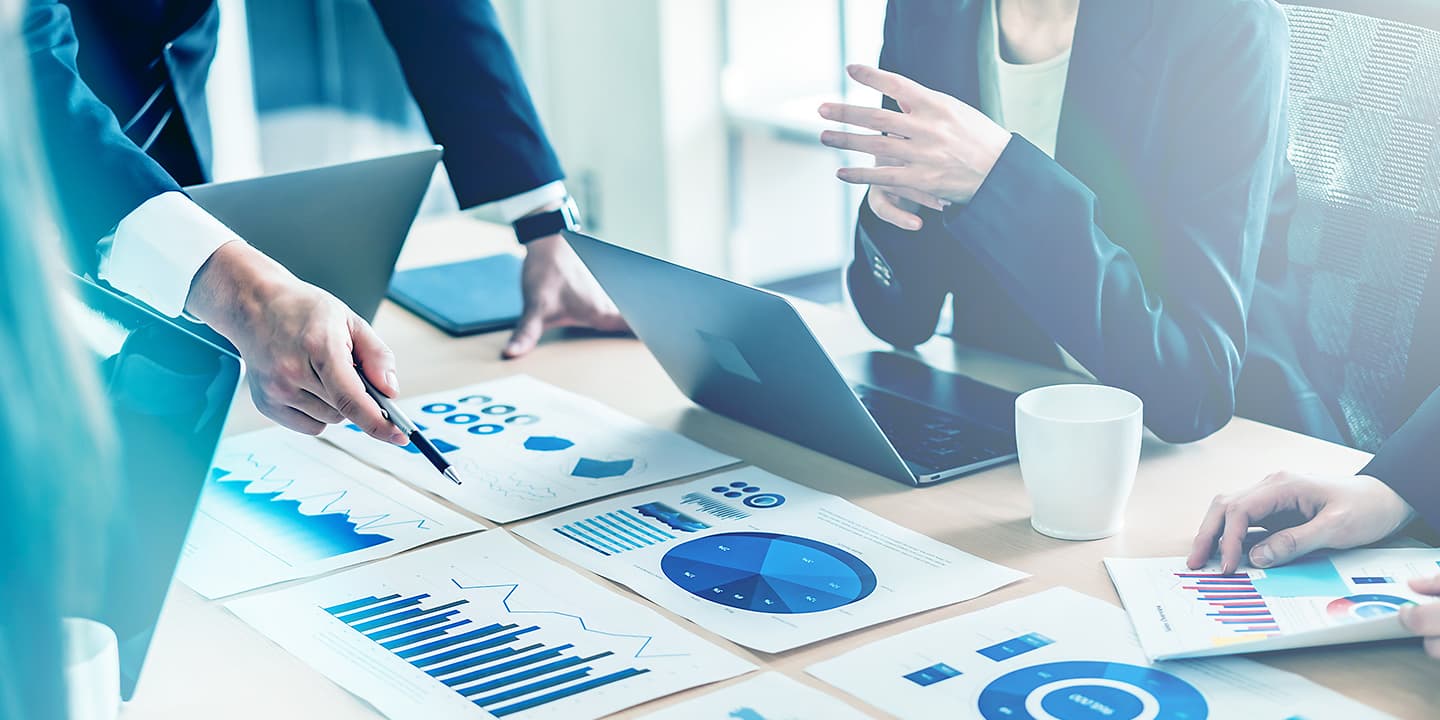
IoT化導入のステップは大きく分けると6つに分類できます。5と6は最先端の技術による、AI活用から自動化まで進む流れですが、一般的に人間が利用するまでは4のシステム導入まで考えれば良いでしょう。
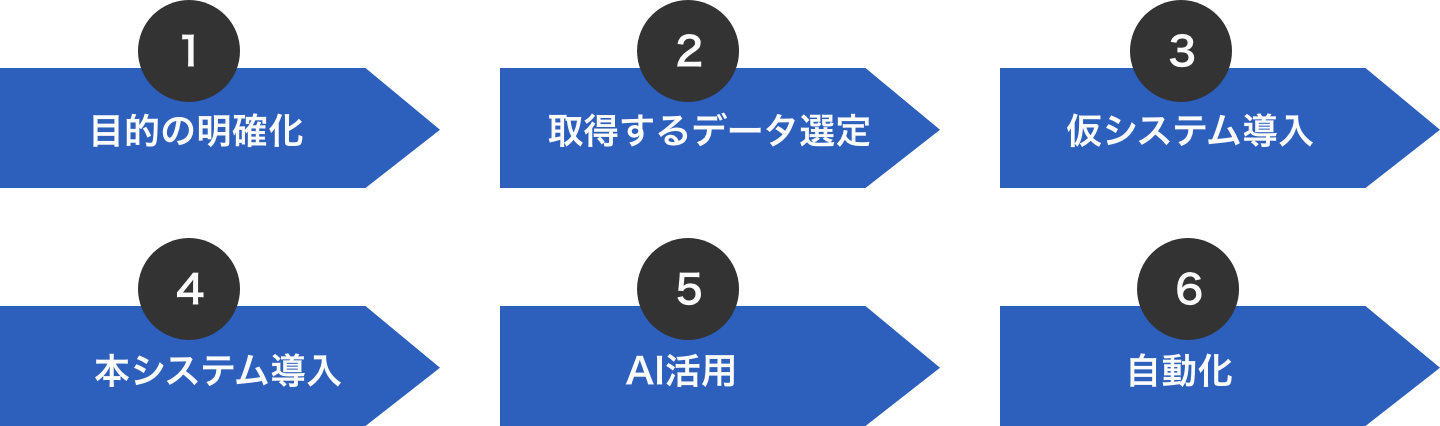
IoT導入の目的明確化
導入目的の整理は、製造業で代表的な観点としては「3現主義(現地・現物・現実)」の考え方が有効です。自社のムダがどこにどれだけあるかを見える化することで、目的が整理できます。
目的 | 排除するべき7つのムダ | 改善後の期待できる効果 |
---|---|---|
在庫を削減 |
|
排除することで初めて後工程から引き取られた物を次工程で与えられた時間の中で生産し安定して供給できるか、前工程から必要な物が適宜供給されているか、といった事項の改善につなげていくことができる。 |
生産性、可動性UP |
|
レイアウト変更により運搬経路を長くしたり、金型の点数が増えることにより外部の倉庫や工程から離れた空きスペースから出し入れする非効率な運搬を改善できる。 |
品質向上 + 品質強化 |
|
現場のレベルアップにつながる |
付加価値 向上の追求 |
|
さらに細かい動作改善を行い、自社の強みを磨いて他社との差別化につなげる |
取得すべきデータの選定
目的を達成するために必要なデータを検討をします。生産ラインの稼働状況、製品の品質データ、原材料の使用量など、収集するデータの種類と量を決めます。
仮システムの組み立てとその評価
主に、PoC(概念実証)の実施を行うことで、小規模な範囲でシステムを導入し、効果を検証します。仮システムの組立と評価の目的は「導入効果の検証」「課題の抽出」「導入計画の策定」です。IoT導入には様々な課題があるため、仮システムでこれらの課題を事前に把握し、本格的なIoT導入に導くことができます。具体的には、導入対象の選定、仮システム構築、仮システム運用、評価のステップで、慎重に実施することで本格的なIoT導入のリスクを軽減し、成功確率を高めることができます。
本システム構築と動作チェック
仮システムで十分に検討した後、本システム構築に入ります。大まかな流れは、設計、開発、テスト、導入、動作チェックになります。具体的には以下の表の内容を中心に検討と実施します。
フェーズ | 項目 | 検討事項・実施内容 |
---|---|---|
システム設計 | 導入するIoTシステムの機能 | 工場で実現したい目的に合わせて、必要な機能を検討。 |
IoTデバイスの選定 | 収集したいデータに合わせて、適切なIoTデバイスを検討。 | |
データ収集・分析の仕組み | 収集したデータをどのように収集・分析するかを検討。 | |
セキュリティ対策 | IoTシステムをサイバー攻撃から守るためのセキュリティ対策を検討。 | |
システム開発 | 要件定義 | データ収集の種類、方法、分析を検討。システム機能、セキュリティの要件整理。 |
システム設計 | 構成、アーキテクチャ、ソフトウェア、ハードウェアなどの選定を検討。 | |
システム開発 | 開発言語、開発環境、開発ツールの選定。開発プロセスの検討。 | |
セキュリティ対策 | IoTシステムをサイバー攻撃から守るためのセキュリティ対策を検討。 | |
システムテスト (動作チェック) |
機能テスト | IoTシステムが正常に動作するかをテスト |
性能テスト | IoTシステムが想定される負荷を処理できるかを確認 | |
セキュリティテスト | IoTシステムがサイバー攻撃から守られているかを確認 | |
システム導入 | システムの設置場所 | 工場内の設置場所を検討 |
システム運用体制 | IoTシステム運用体制の構築を検討 | |
システムの教育 | 利用する従業員に教育開始 |
本システム構成から動作チェックまでのポイントは3点です。まず導入するIoTシステムの機能や仕様を十分に検討しテストを行うこと、つぎに現場の声を反映して改善すること、最後にシステム導入後も運用体制を整えて、継続的に運用と改善をはかること。このポイントを抑えることで、工場の生産性や品質の向上に繋がることが期待できます。
データのAI活用(見える化・分析)
製造業における工場などで利用されるAIは、人間のような意識を持つ「汎用型AI」ではなく、意識のない「特化型AI」を利用することが多いです。特化型は、特定の分野やタスクに特化したAIですので、生産ライン自動化や品質管理など、異なるデータや技術に対応することができます。一方で数は少ないですが、汎用型の需要予測や在庫管理などデータ分析が中心となる業務では、人間のサポート的な位置づけで利用されることもあります。IoT技術で工場の機器などのモノと通信することで、クラウドに蓄積されたビックデータをAIで分析・解析し「見える化」します。見える化されたデータをもとに問題点を洗い出し、業務改善や製造工程の改善に伴い生産性向上が期待できます。
自動化・自律化を実現する生産設備の制御
工場のIoT化により、予兆検知制御、最適制御、自律制御の3点が可能になります。具体的には、設備の故障や異常を予兆的に検知し、自動的に停止や制御を行い、稼働率や品質向上に繋げることができます。また、収集したデータをもとに、最適な運転条件を自動的に設定する制御で、エネルギー効率や生産性工場に繋がります。さらには環境や状況に応じて、自律的に制御を行い、作業者の負担軽減や新たな価値創造にも繋がります。例えば、ロボット活用による自動化を進めることで作業者の負担軽減や、AI活用で人間が思いつかなかった新しい発見を生み出すことも期待できます。
工場IoTの可能性と未来の工場について
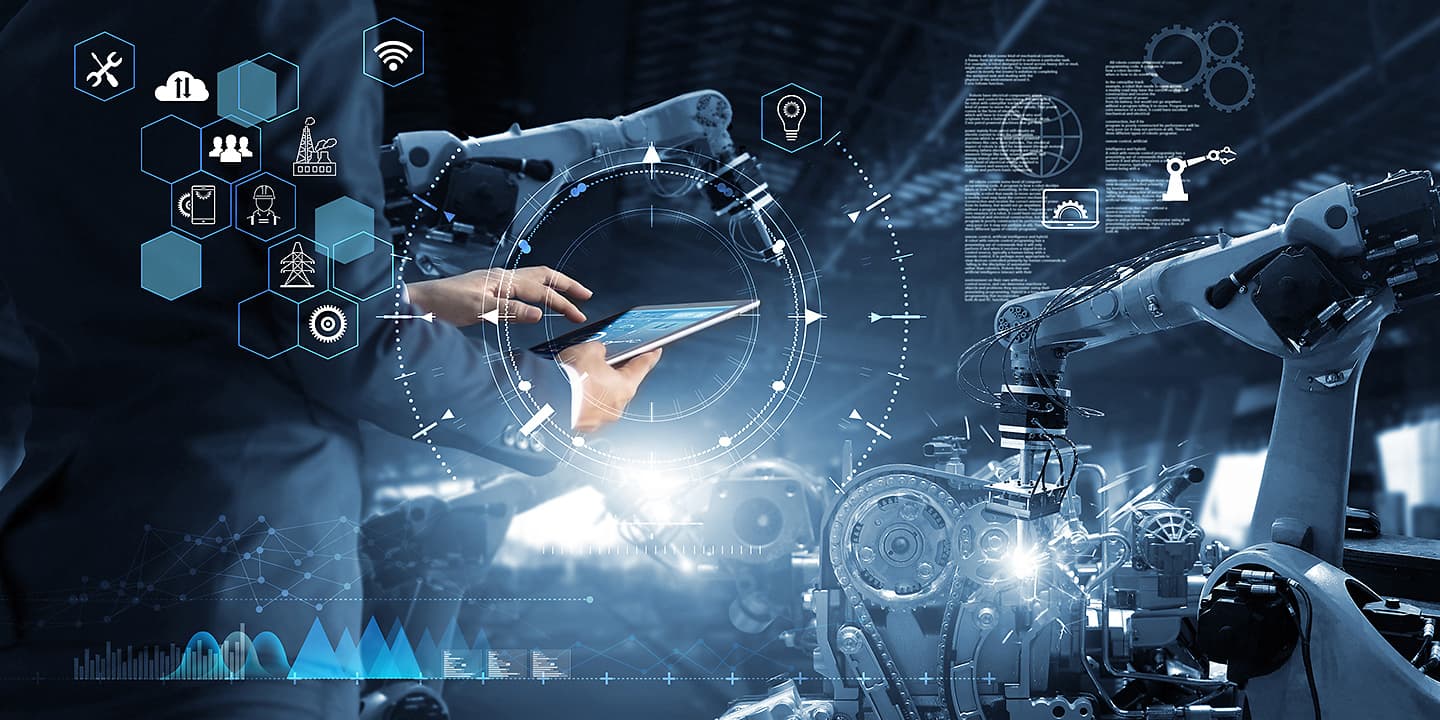
日本でもインダストリー4.0、インダストリアル・インターネットに匹敵する産学官連携プロジェクトが始動しています。日本政府は2016年1月に「第5期科学技術基本計画」として「Society5.0(読み:ソサエティ5.0)」の概念を閣議決定しています。狩猟社会、農耕社会、工業社会、情報社会に次ぐ第5の社会を生み出す変革と言われ、「人間中心社会」とよばれるものです。IoTが実現するSociety5.0が目指す社会は、サイバー空間とフィジカル空間が高度に融合し、経済発展と社会的課題の解決が両立した新たな社会のことです。IoTは、Society5.0の実現に欠かせない技術であり、その可能性は非常に広大です。製造業では生産効率の向上や、物流の効率化を目指すことが主な目的となります。具体的には製造現場のIoTデバイスに取り付けられているセンサーやカメラ、RFIDタグのあらゆる機器や設備からデータを収集し、分析することで、生産性の向上や品質の改善、コスト削減などの効果を期待できます。
工場とIoTの未来像
未来のスマート工場は、今後数十年で「協調ロボット」「金属3Dプリンター」「IoT」「AI」「ビッグデータ処理」「RPA」などの分野において技術の進化が進むと予想されています。今後の日本社会は少子高齢化が進み作業者も高齢化が進むためIoTやAIの活用に進化させることで、将来は無人化工場の実現も現実味を帯びてきます。工場管理の「生産管理」「購買・在庫管理」「倉庫管理」「原価管理」「人事管理」などの工場要員もIT化、IoT、RPAの活用進化で無人化が実現できるようになるでしょう。工場の管理は遠隔監視で、工場の無人化自動運転や生産技術研究所、製品開発拠点、リモート監視設備などが主体となる工場設備が敷地内に存在しているかもしれません。
IoTがもたらす可能性
製造/資源セクターにおける支出額について、2022年の実績(見込み値)は2兆4,193億円であり、その後、2022年~2027年のCAGR 8.4%で成長し、2027年には3兆6,219億円に達すると予測しています。市場の成長とともに製造業のIoTは、これからも成長を続けていくことがわかります。
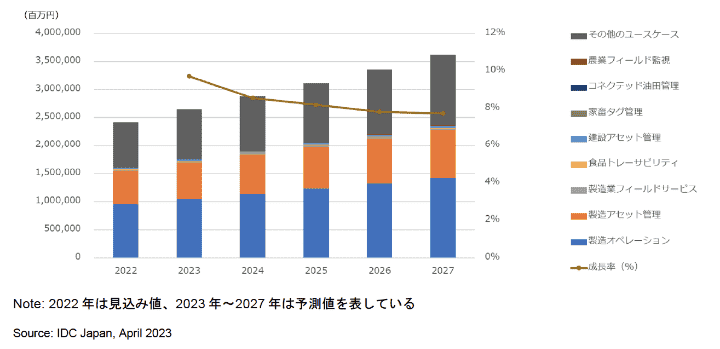
製造業では「さまざまなモノやヒトなどからデータを得て処理し、現実世界でフィードバックする」一連の活動が成果を生むと言われており、現実世界に対して新たな価値を生み出すことが肝心です。またこれにより「オーダーメイド」と「アフターサービス」を重視できるビジネスモデルに変革できる可能性があります。製造現場だけではなく、製造業はIoTを通じてビジネスモデルを変革する大きな可能性を秘めています。
工場の自律化の進行とIoTの役割
工場における自律化は、従来人間が行ってきた「勘と経験と匠の技」のような属人化したものではなく人工知能(AI)でサポート、「深層学習」で打ち手を示唆のような考え方に変わります。IoTデジタル技術で人間の5感の役割を担い、深層学習(ディープラーニング)を活用し汎用的な考え方を構築します。人工知能で技能を継承し向上させ省人化、省力化の実現が、IoTとビッグデータとAIを活用し現場にフィードバックし改善を続けることで、最終的には工場の自律化がゴールとなります。
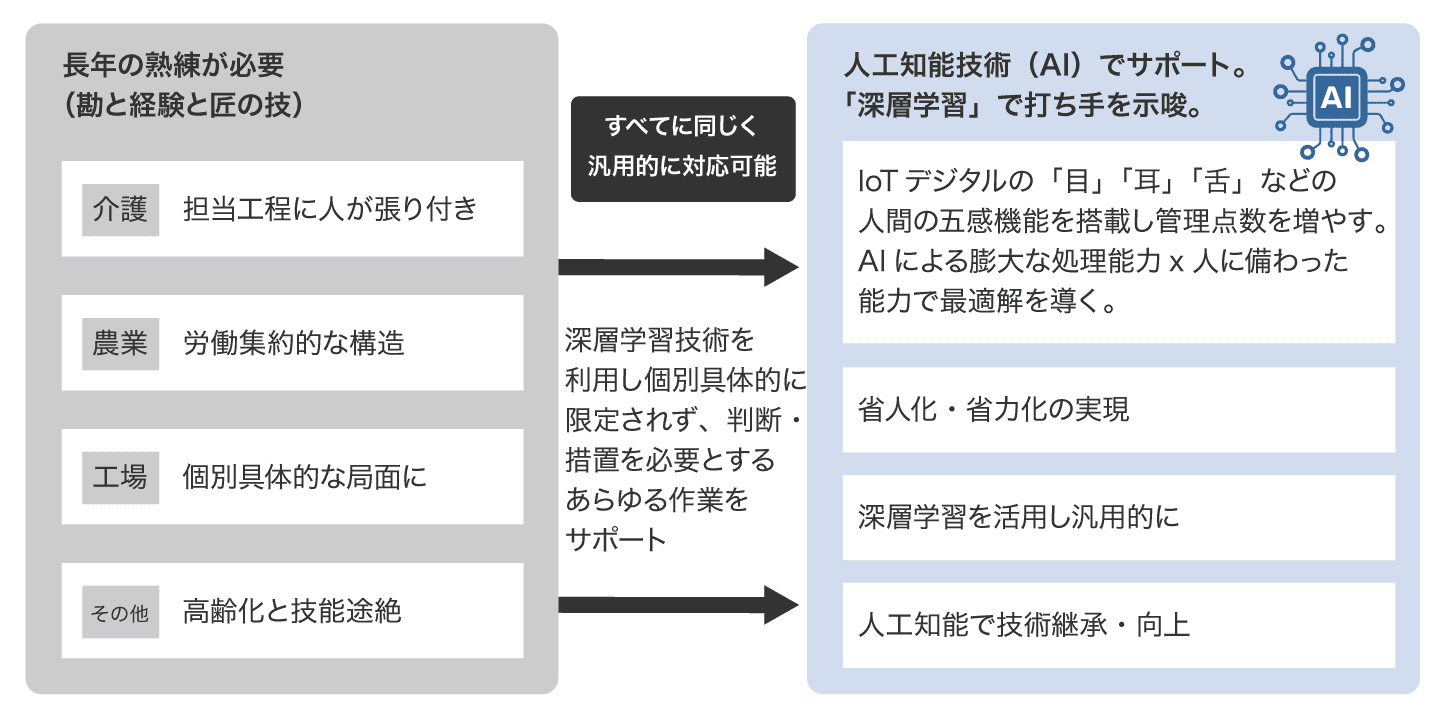
未来の工場(これからのIoT活用が必須)
IoTを活用した工場では、省人化、省力化がすすむとともに、AIで技能の継承と向上により精度がアップします。また、原価や在庫管理コストの削減や納期の正確性も向上し未来の工場(スマートファクトリー)は主要KPIが格段に変わることが予測できます。これらの取り組みから大幅な数値改善に繋がり、安全性、生産性、収益性の向上につながることでしょう。
IoT通信についてもっと知りたい方へ
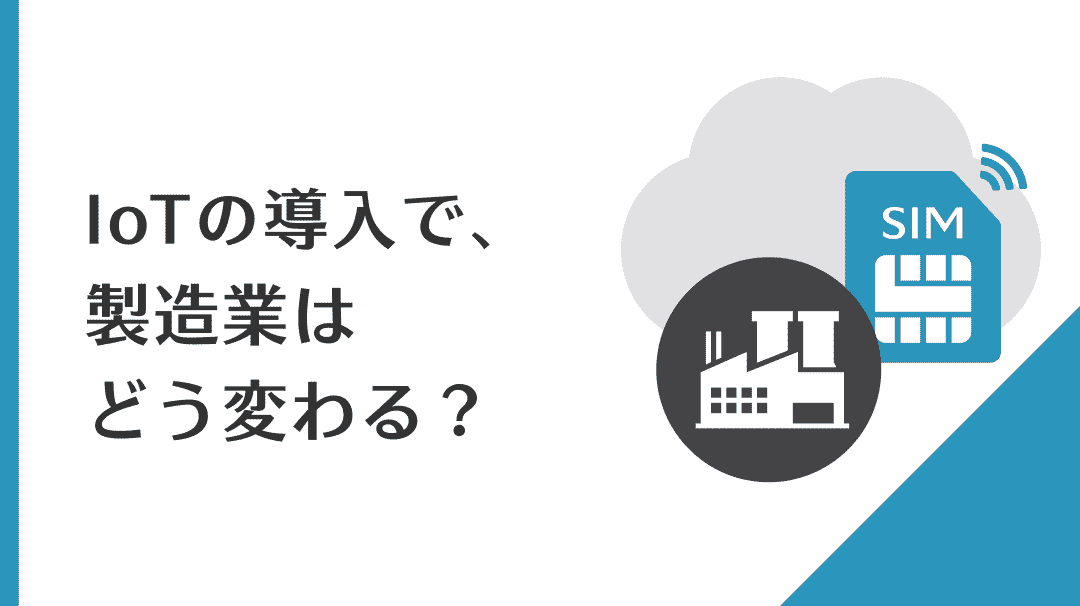
製造業界でも近年はIoTの導入が増加しています。生産ラインの効率化、品質管理、定点観測に対して、IoTの組み込みが行われています。資料では製造業のIoTネットワークに関する導入メリットをご紹介します。
- 図解即戦力 IoT開発がこれ1冊でしっかりわかる教科書 IoT検定パワーユーザー対応版(技術評論社)
- 図解即戦力IoTのしくみと技術がこれ1冊でしっかりわかる教科書IoT検定パワーユーザー対応版(技術評論社)
- 図解即戦力 AIの仕組みがしっかりわかる教科書(技術評論社)
- 60分でわかる! IoTビジネス最前線[改訂2版] (60分でわかる! IT知識)(技術評論社)
- IoTで激変する日本型製造業ビジネスモデル(日刊工業新聞社)
- 製造業のIoT活用Q&A(日課議連)
- イラスト図解 スマート工場の仕組み(日本実業出版社)